配管溶接とは
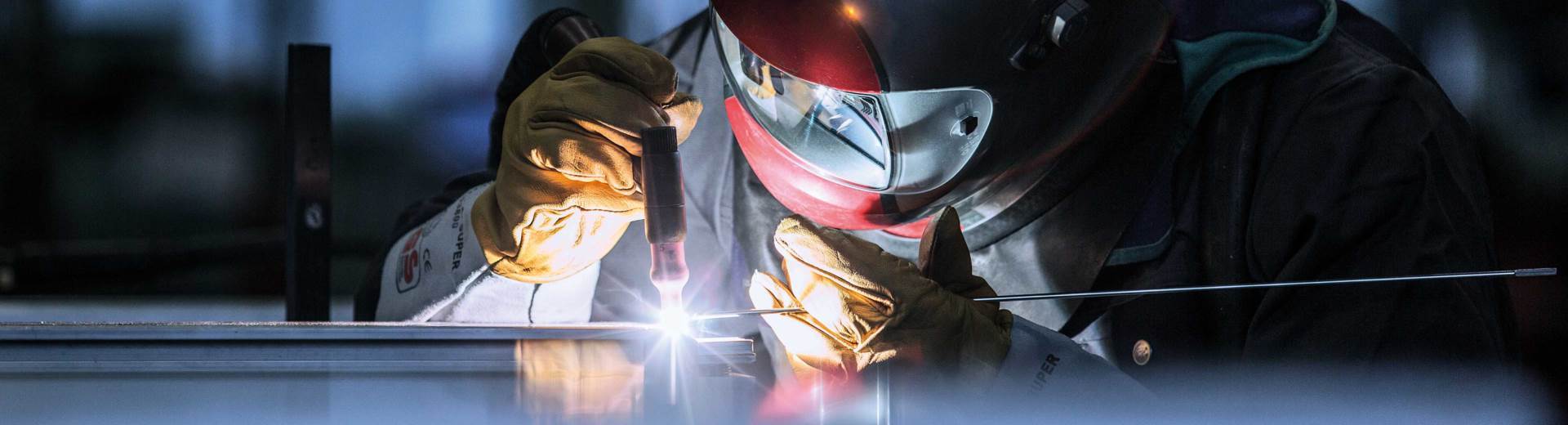
パイプ溶接、これは極めて実用性と普遍性のある技術であり、それはパイプの接続と成形に関係している。あなたにとって、この技術を深く研究し、把握することは、配管工事の円滑な施工を確保するために計り知れない意義があります。今、私はあなたを全面的にパイプ溶接の世界に連れて行って、一緒にその中の知識の奥義を探します。
配管溶接とは?
パイプ溶接とは、パイプの両端を溶接により接続する接続方法のことです。配管業界で最も一般的な接続方法の1つであり、溶接の強度が高く、密封性がよく、耐食性が高いなどの利点がある。
1.パイプ溶接前の準備:
1.1 溶接原材料
配管溶接に関わると、どのような原材料が必要なのか気になるかもしれません。まず、溶接電源は、溶接に必要な電気エネルギーを提供する必要があります。次に、溶接の強度とシール性を確保するために、充填材として溶接に追加される適切な溶接棒または溶接ワイヤを選択する必要があります。また、シールドガスも重要な一環であり、溶接領域を保護し、不純物や酸素による溶接の汚染を防止するのに役立ちます。
溶接材料の分類において、狭義には、溶接材料とは、主に溶接ビード、積層層層層、ろう材に充填するための金属合金材料を指す。これには、さまざまなワイヤと溶接棒、およびろう付けに使用されるろう材が含まれます。一方、広義の意味では、溶接原材料はより広く、溶接棒と溶接ワイヤのほか、金属粉末、溶接剤、溶接時に必要なガスなども含まれている。これらの原材料は共同で完全な溶接材料システムを構成し、パイプ溶接の品質と効率を確保している。
ようせつぼう
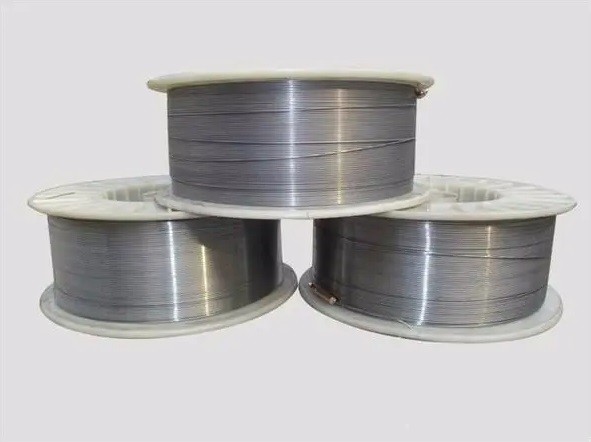
一般的に使用される溶接ワイヤには、酸化アルミニウムネオジム、酸化アルミニウムジルコニウム、酸化アルミニウムバリウム、純マグネシウムなど様々な種類がある。 その中でも、酸化アルミニウムネオジム系ワイヤーは、より広く使用されているワイヤーの一つです。
溶接棒
溶接棒とは、ガス溶接や電気溶接の際に、 溶融して被溶接物の接合部に充填される帯状の 金属である。 電極の材質は通常、被加工物の材質と同じである。 溶接棒は、電極アーク溶接用のフラックスを塗布した溶融電極で、フラックスとコアの2つの部分から成る。
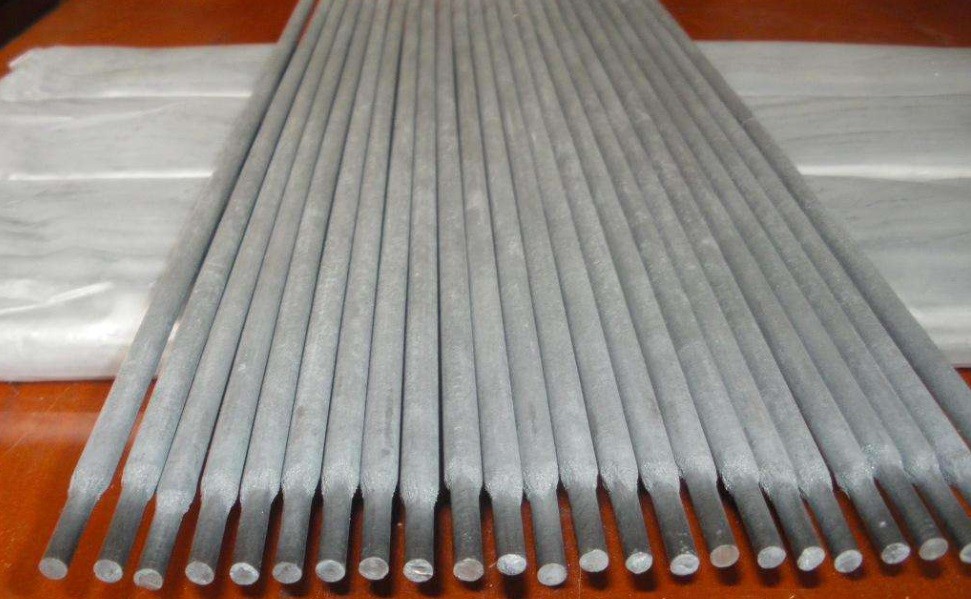
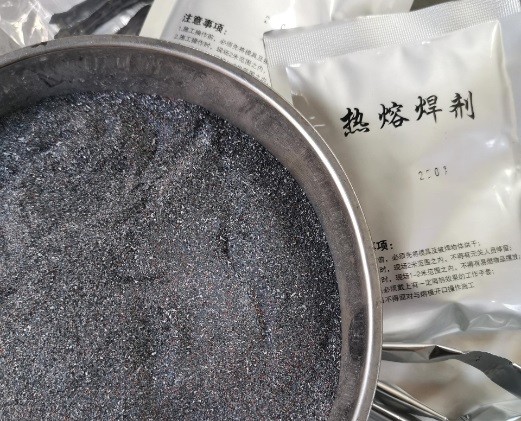
ようせつざい
フラックスはろう剤とも呼ばれ、溶融塩、有機物、活性ガス、金属蒸気など、すなわち母材とろう材を除去する以外に、母材とろう材の界面張力を低下させるために使用される第3のすべての物質を指す。
シールドガス
パイプ溶接にはシールド・ガスも必要で、通常 はアルゴンやアルカンなどの不活性ガスが使われる。 シールド・ガスは、溶融池と溶接部 を空気中の酸化から保護し、溶接の品質を保証す る。
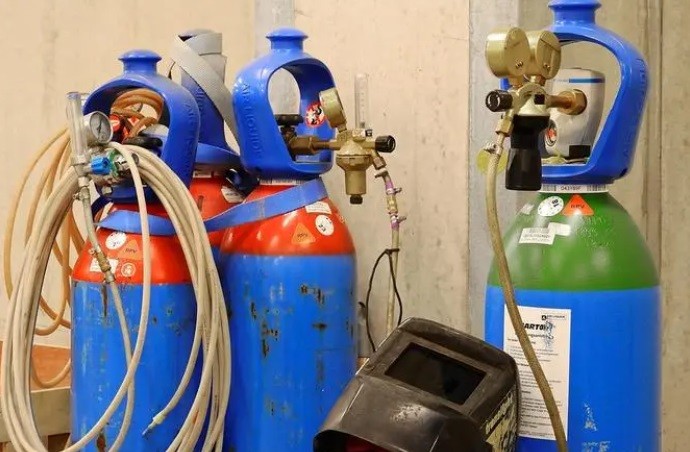
1.2 溶接電源の種類
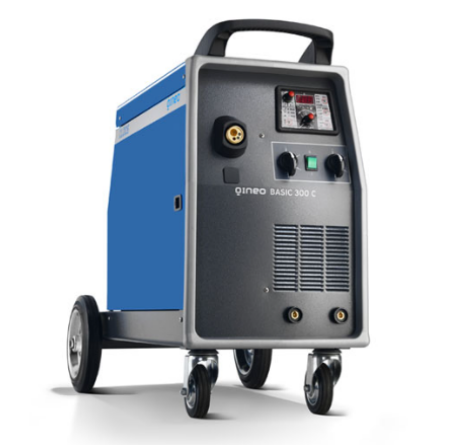
溶接電源の種類:交流、直流
溶接電源は溶接の核心設備である。 現在、主に直流電源、交流電源、パルス電源などが市販されています。 どのタイプの溶接電源を選択するかは、実際の溶接状況に応じて決定する必要があります。 通常、小さいパイプでは直流溶接で十分です。 太いパイプでは、交流電気溶接またはパルス電源が必要です。
1.3 極性選択

原則
正接:溶接部品は電源正極に接続し、溶接棒は電源負極に接続する配線方法。
逆接:溶接部品は電源負極に接続し、溶接棒は電源正極に接続する配線方法。
極性選択の原則:
アルカリ溶接棒は常に直流逆接合を採用し、そうしないと、アーク燃焼が不安定で、スパッタが深刻で、騒音が大きい。
酸性溶接棒に直流電源を使用する場合は、通常直流正接を使用します。
1.4 研削工具
研削具はパイプ溶接に欠かせないツールである。溶接後、溶接継ぎ目を磨き、継ぎ目を滑らかにする必要があります。これにより、配管の美観性及び溶接平坦性を向上させることができる。一般的な研削具には、角研削機、ヤスリ、サンドペーパーなどがあります。
写真は3枚で、それぞれ角研削機、ヤスリ、サンドペーパーです。
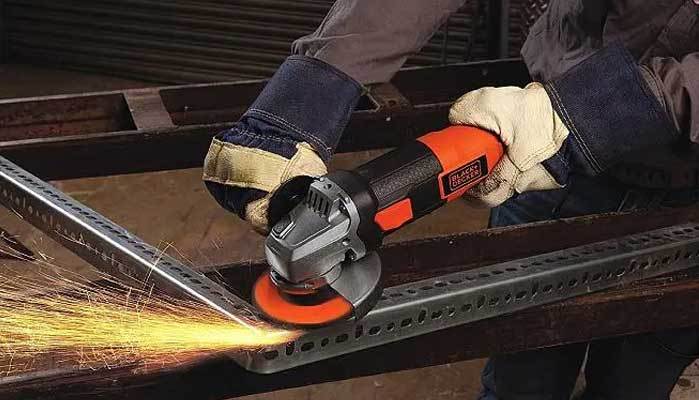
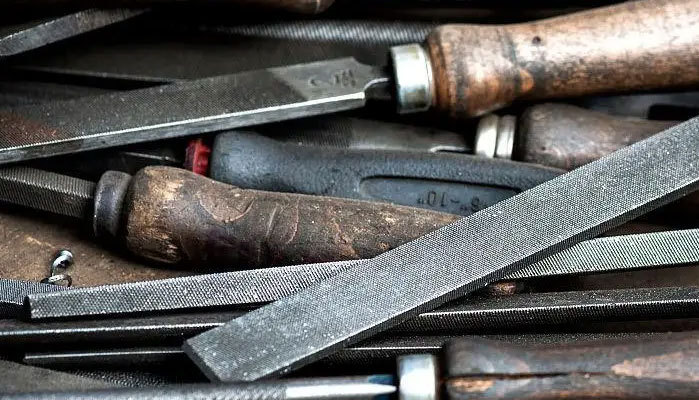
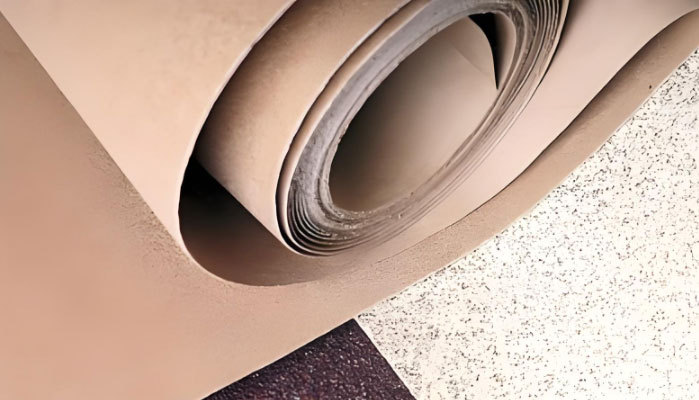
1.5 保護具
溶接管の溶接は技術と危険に満ちた仕事であり、溶接された防護服、防護手袋、防護マスク、防護靴などを準備して着用しなければならない。
写真4枚は、防護マスク、防護靴、防護手袋、防護服。
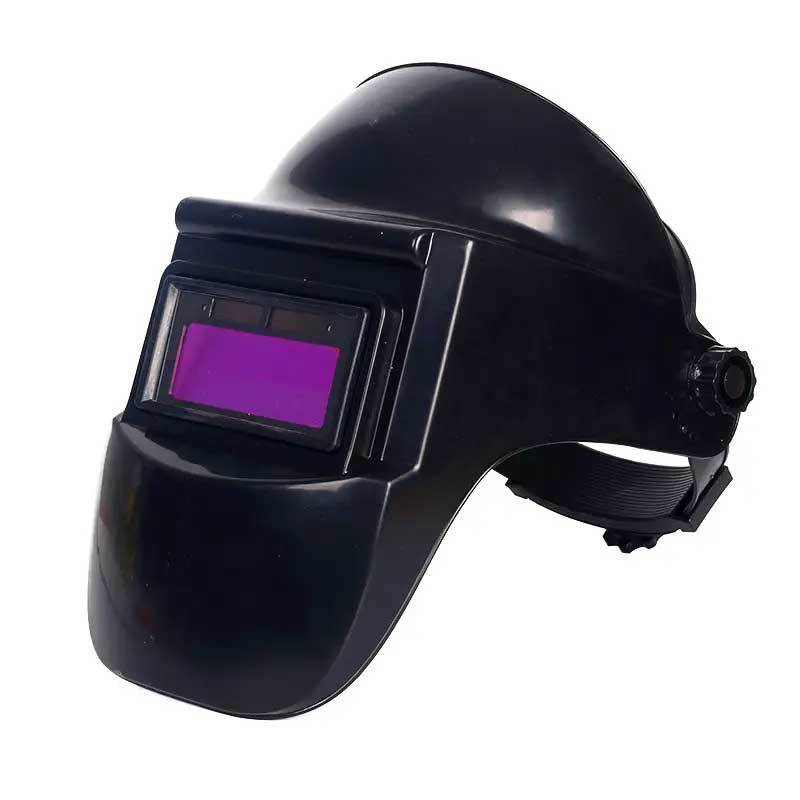

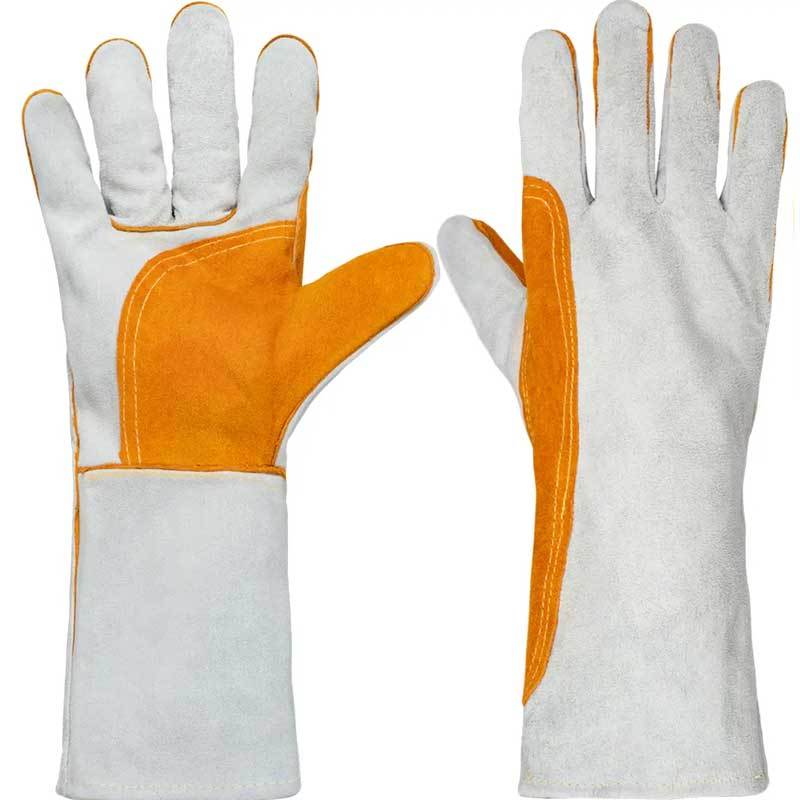

2. パイプ溶接タイプ
溶接タイプリレーショナルネットワーク
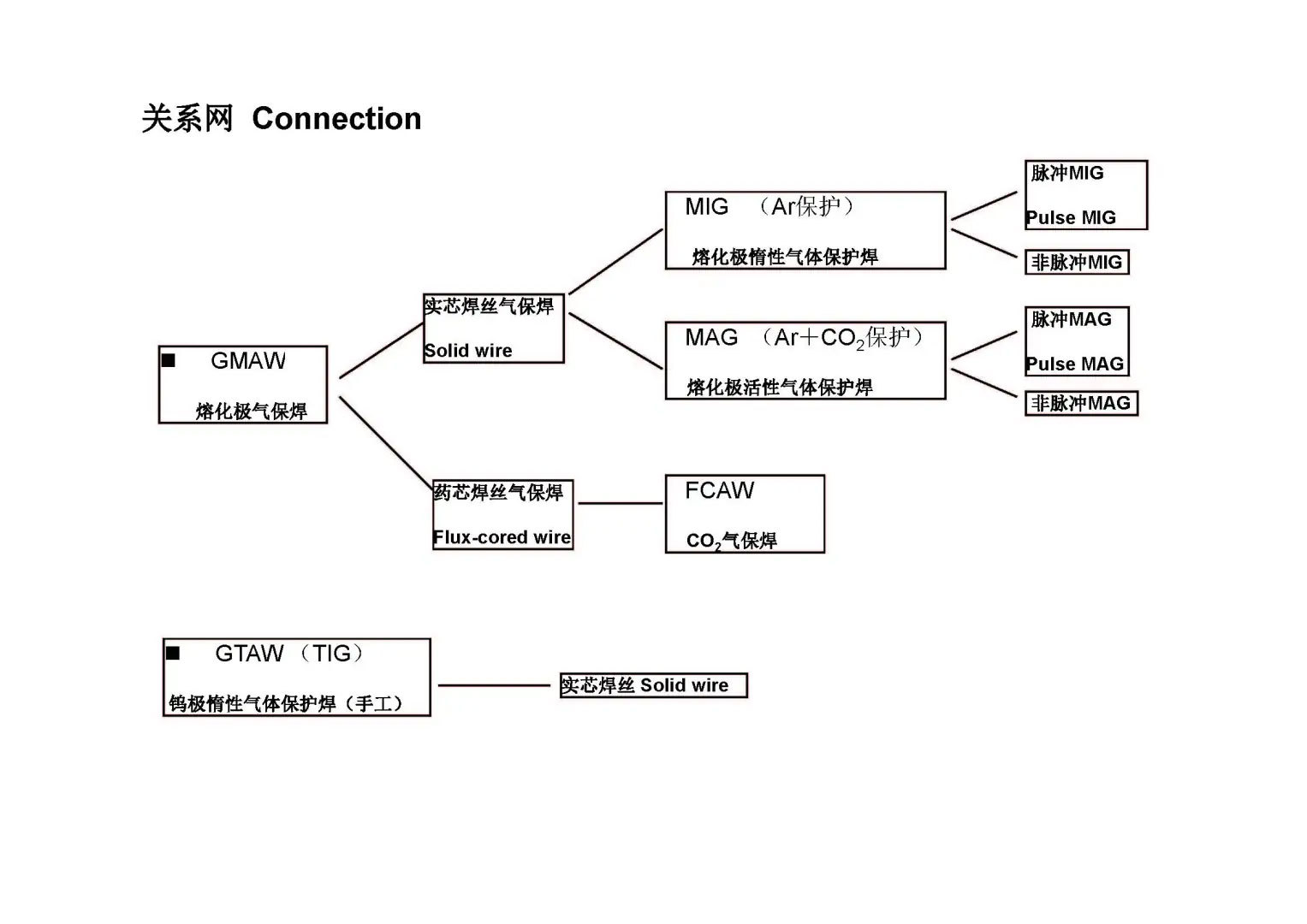
2.1 溶接棒アーク溶接(SMAW)手動溶接方法

SMAW
アークを熱源溶融ビードとして母材と溶接ビードを形成する手作業溶接方法であり、アーク温度は6000〜8000℃程度である。黒色金属及び一部の非鉄金属の溶接に適しており、応用範囲は非常に広く、特に短溶接、不規則溶接に適している。
2.1.1 利点
(1)技術技術が柔軟で、適応性が強く、炭素鋼、低合金鋼、耐熱鋼、低温鋼とステンレス鋼などの各種材料の平、横、立、仰向けの各種位置及び異なる厚さ、異なる構造の溶接部品形状の溶接に適用する。
(2)ガス溶接及び埋め込みアーク溶接に比べて、金相組織が細く、熱影響領域が小さく、継手の性能が良い。
(3)プロセス調整(対称溶接など)による応力の制御と変形の改善が容易である。
(4)設備が簡単で、操作が便利である。
2.1.2 デメリット
(1)溶接技術に対する要求が高い。溶接工の操作技術と経験は製品の品質に直接影響する。
(2)労働条件が悪い。溶接工は仕事をする時に手と脳を併用しなければならず、精神が高度に集中しており、しかも高温焼成及び有毒ガス、煙塵、金属蒸気の危害を受けなければならない。
(3)生産性が低い。溶接工の体質の影響を受け、溶接パラメータの選択範囲が小さいため、生産性が低い。
2.1.3 応用範囲
溶接電極アーク溶接は、造船、ボイラーおよび圧力容器、機械製造、建築構造物、化学装置、その他の製造および保守産業で広く使用されている。
2.2 溶融極ガスシールド溶接(GMAW)
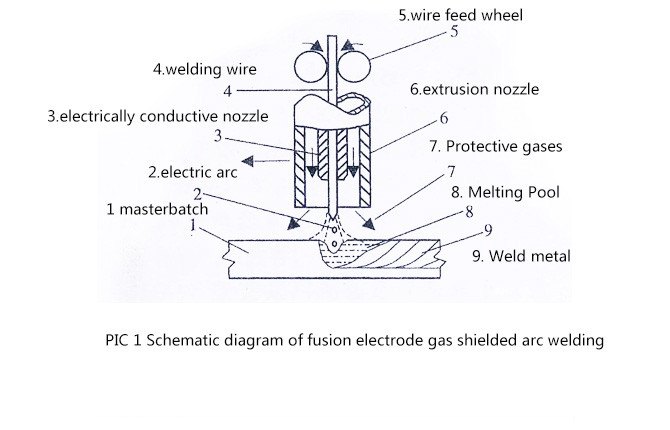
GMAW
溶融可能なワイヤと被溶接ワークとの間に連続等速送りされるアークを熱源としてワイヤと母材金属を溶融し、溶融池と溶接ビードを形成する溶接方法である。良好な溶接ビードを得るためには、アーク媒体として外加ガスを利用し、溶滴、溶融池金属及び溶接区の高温金属を周囲空気の有害作用から保護しなければならない。
2.2.1 利点:
溶融極ガス保護溶接とスラグ保護溶接方法(例えば溶接棒アーク溶接と埋め込みアーク溶接)を比較して、技術上、生産性と経済効果などの面で以下の利点がある:
(1)ガスシールド溶接はアーク溶接である。溶接過程におけるアーク及び溶融池の加熱溶融状況がはっきりしており、問題を発見し、適時に調整するのに便利であるため、溶接過程と溶接品質は制御しやすい。
(2)ガスシールド溶接は通常の場合、管状ワイヤを採用する必要がないため、溶接過程にスラグがなく、溶接後にスラグを不要にし、スラグの補助工数を省き、溶接コストを低減する。
(3)適用範囲が広く、生産効率が高く、全位置溶接を行いやすく、機械化と自動化を実現する。
2.2.2 欠点:
溶融極ガス保護溶接の不足点:溶接時に明るいアークと使用する電流密度が大きく、アーク光放射が強い、次に、風のある場所や露天での溶接には適していない、設備が複雑である。
2.2.3 応用範囲:
ほとんどの金属と合金の溶接に適しており、炭素鋼と低合金鋼、ステンレス鋼、耐熱合金、アルミニウムとアルミニウム合金、銅と銅合金とマグネシウム合金の溶接に最適である。
高強度鋼、超強アルミニウム合金、亜鉛含有量の高い銅合金、鋳鉄、オーステナイトマンガン鋼、チタンとチタン合金及び高融点金属に対して、溶融極ガス保護溶接は母材を予熱及び溶接後に熱処理し、特製の溶接ワイヤを採用し、保護ガスを制御することは通常よりも厳格である。
鉛、スズ、亜鉛などの低融点金属に対しては、溶融極ガス保護溶接を採用することは好ましくない。このような金属を表面被覆するコーティング鋼板も、このような溶接方法を採用するのに適していない。
2.2.4 カテゴリ:
溶融極ガスシールド溶接は、溶融極不活性ガスシールドアーク溶接(MIG)、活性ガスシールドアーク溶接(MAG)、二酸化炭素ガスシールドアーク溶接(二酸化炭素溶接)に分けることができる
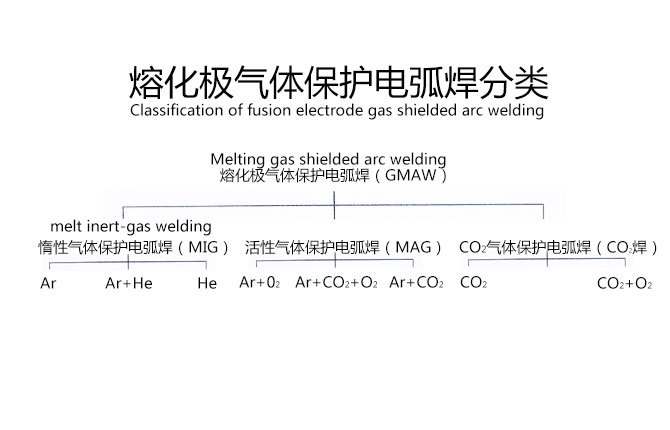
2.2.4.1 溶融極不活性ガス保護アーク溶接MIG
溶融極アルゴンアーク溶接は、溶融電極としてワイヤを用い、保護ガスとしてアルゴンガスまたはアルゴンリッチ混合ガスを用いたアーク溶接方法であり、保護ガスが不活性ガスArまたはAr Heである場合、一般に溶融極不活性ガス保護アーク溶接と呼ばれ、MIGと略称される。MIG溶接はステンレス鋼やアルミニウム、銅などの非鉄金属の溶接に適している。低炭素鋼にとっては高価な溶接法である。
2.2.4.1.1 利点
(1) MIG 溶接シールド ガスはない酸化純粋な不活性ガス、アーク スペースなし酸化を避けることができる、溶接スラグを生成しません、ワイヤの脱酸素剤を追加する必要はありません、ワイヤ溶接の基材と同じ組成を使用できます;MAG 溶接シールド ガス酸化が、比較的弱い。
(2)は二酸化炭素のガスによって保護されるアーク溶接、溶融アーク溶接アークの安定性、美しい形作る溶接スパッターより少なく溶接する液滴の安定した転移と比較した。
(3)は電極、ワイヤーおよびアークの流れ密度、ワイヤー溶ける速度、高い沈殿率、融合の基材の深さ、溶接の変形としてワイヤーの使用による TIG 溶接、融合の電極アーク溶接と小さいです、高い溶接の生産比較しました。
(4)アルミニウムおよびアルミ合金を溶接する肯定的なDCアークのためのMIG溶接ワイヤー、基材の表面の酸化膜はよい陰極清浄効果を有する。
2.2.4.1.2 欠点
(1)アルゴンガス及び混合ガスはいずれもCO 2ガスの販売価格より高いため、溶接コストはCO 2ガス溶接の溶接コストより高い。
(2)MIG溶接はワーク、溶接ワイヤの溶接前整理に対する要求が高く、すなわち溶接過程は油、さびなどの汚染に敏感である。
2.2.4.1.3 適用範囲
ほとんどすべての金属材料を溶接することができ、広く応用されている。
2.2.4.2 MAG活性ガス保護アーク溶接
MAG(Metal Active Gas Arc Welding)溶接は、溶融極活性ガス保護アーク溶接の英語略称である。アルゴンガスに少量の酸化性ガス(酸素、二酸化炭素、またはその混合ガス)を加えて混合した混合ガス保護溶接である。わが国でよく使われているのは80%Ar+20%二酸化炭素の混合ガスであり、混合ガス中のアルゴンガスの占める割合が大きいため、アルゴンリッチ混合ガス保護溶接とよく呼ばれる。
2.2.4.2.1 利点
(1) 溶滴遷移の安定性を向上させる。
(2) カソードスポットを安定させ、アーク燃焼の安定性を向上させる。
(3) 溶接深さと外観の形状を改善する。
(4) アークの熱出力を高める。
(5) 溶接の冶金的品質を管理し、溶接欠陥を減らす。
(6) 溶接コストの低減
2.2.4.2.2 欠点
ガス保護性が低い:活性ガス(二酸化炭素など)は不活性ガスのように空気中の酸素と水蒸気を完全に遮断することができないため、溶接部にはより多くの気孔と不純物がある可能性がある。
溶接外観:不活性ガスを用いたMIG溶接に比べて、MAG溶接の溶接外観はやや劣る可能性があり、より多くの後処理が必要である可能性がある。
アーク安定性:純二酸化炭素を使用する場合、アーク安定性は相対的に悪く、スパッタが発生しやすい。
2.2.4.2.3 適用範囲
MAG溶接のプロセス内容とプロセスパラメータの選択原則はMIG溶接と似ている。溶接前のクリーニングはMIG溶接の要求ほど厳しくない。
MAG溶接は主に炭素鋼、合金鋼、ステンレス鋼などの黒色金属の溶接に適用され、特にステンレス鋼の溶接に広く応用されている。
2.2.4.3 二酸化炭素ガスシールドアーク溶接
二酸化炭素ガスシールド溶接はアークを用いて高温を形成するとともに、ガス(CO 2)を添加することにより溶接部位への空気の侵入を防止する。この溶接方法はその高効率、低コスト、成形美観のために広く応用されている。次に、二酸化炭素ガスシールド溶接の応用とメリットとデメリットについて説明します。
2.2.4.3.1 利点
1.二酸化炭素ガスシールド溶接は溶接速度が速く、効率が高い利点がある、
2.二酸化炭素ガス保護溶接のコストが安く、大規模機械生産と都市建設などの分野で大規模に応用できる、
3.二酸化炭素ガス保護溶接は溶接品質が高く、溶接継ぎ目が美しいなどの特徴がある。
2.2.4.3.2 欠点
1.ガス過程によりレーザー光の折り返しとレーザー波が溶接過程で歪みが発生し、品質変動が発生する、
2.二酸化炭素ガスシールド溶接は溶接シーンに対する要求が高く、ガス処理プロセスが複雑である。専門のオペレータによる操作が必要です。
2.2.4.3.3 適用範囲
二酸化炭素ガス保護溶接は、橋梁、自動車、船舶、鉱山機械、建築構造、送油管などのさまざまなタイプの鋼構造溶接に応用することができる。溶接中、ガスは効果的に溶接部位と周囲の空気を隔離し、溶接品質を保証すると同時に、溶接をより美しくする。
2.3 フラックス入りワイヤアーク溶接(FCAW)
フラックス入りワイヤアーク溶接は、フラックス入りワイヤとワークとの間のアークを用いて加熱する溶接方法であり、英語名の略称はFCAWである。アーク熱の作用下で、ワイヤ金属及びワークが接続される部位が溶融し、溶融池が形成され、アークが前進した後に溶融池の尾部が結晶化して溶接ビードが形成される。
フラックス入りワイヤガスシールド溶接の基本的な動作原理は、通常の溶融極ガスシールド溶接と同様に、溶融可能なフラックス入りワイヤを1つの電極(通常は正極、すなわち直流逆接続)とし、母材を別の極とする。通常、保護ガスとして純CO 2またはCO 2+Arガスが用いられる。通常の溶融極ガスシールド溶接との主な違いは、ワイヤ内部にフラックス混合物が入っていることである。溶接時、アーク熱作用下で溶融状態のフラックス材料、ワイヤ金属、母材金属と保護ガスの相互間に冶金作用が発生し、同時に薄い液状スラグが溶滴を被覆し、溶融池を被覆し、溶融金属に対してさらに一層の保護を形成した。実質的にこの溶接方法はガススラグの共同保護方法である。
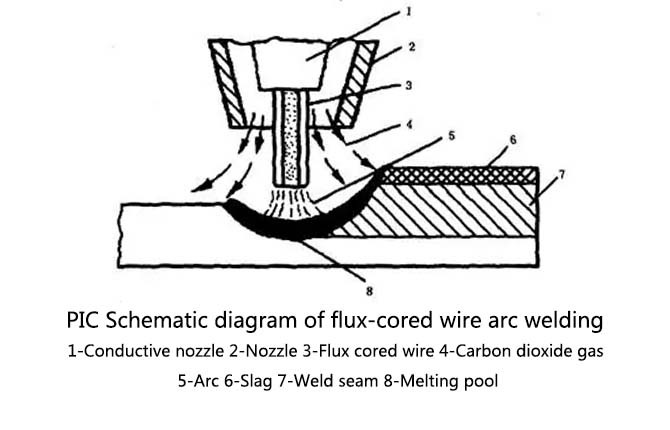
2.3.1 利点
フラックス入りワイヤアーク溶接は、手動アーク溶接と通常の溶融極ガス保護溶接の利点を統合している。主な利点は、
(1)ガススラグ連合保護を採用し、溶接ビードの成形が美しく、アーク安定性がよく、スパッタが少なく、粒子が細かい。
(2)ワイヤは溶着速度が速く、溶着効率(約85%〜90%)と生産性が高い(生産性は手作業溶接より3〜5倍高い)。
(3)各種鋼材を溶接する適応性が高く、フラックスの成分と割合を調整することにより、要求される溶接金属化学成分を提供することができる。
(4)溶接効率が高く(溶接棒に比べて)、自動溶接半自動溶接或いは全自動溶接に適用する。
(5)溶接利用率が高く(溶接棒と比較して)、ワイヤで溶接利用率が電気溶接棒をはるかに上回って、同じ重量で、ワイヤは溶接棒より性価比が高い。
2.3.2 欠点
(1)溶接ワイヤの製造過程が複雑である。
(2)ワイヤ送給はソリッドワイヤより困難であり、ワイヤ送給圧を低減するワイヤ送給機構などを採用する必要がある。
(3)ワイヤの外観は錆びやすく、粉剤は吸湿しやすいため、ワイヤの保存を厳重に管理する必要がある。
2.3.3 応用
フラックス入りワイヤ・アーク溶接は、半自動溶接と自動溶接の両方に使用できるが、通常は半自動溶接に使用される。
配管溶接:配管工事において、薬芯溶接棒は広く溶接配管システム、例えば石油、天然ガス、化学工業配管などに用いられる。これらは信頼性の高い溶接継手を提供し、配管システムのシール性と耐食性を確保することができます。
自動車の製造と修理:自動車の製造と修理の分野では、フラックス溶接棒は通常、自動車の車体、シャーシ、ドア、屋根などの部品を溶接するために用いられる。それらは高品質の溶接継手を提供し、自動車構造の強度と安全性を保証することができる。
2.3.4 セキュリティ操作
フラックス入りワイヤアーク溶接の安全操作技術と操作手順は以下の通りである。
(1)フラックス入りワイヤをアーク溶接する場合、アーク温度は約8000-10000°Cであり、アーク光放射は手動アーク溶接より強いので、防護を強化すべきである。防護服の着用、手袋の着用、防護靴の着用などが必要です。
(2)フラックスコア溶接ワイヤのアーク溶接時、スパッタが多く、特に太いワイヤ溶接(直径1.6 mmより大きい)は、更に大きな粒子スパッタを発生し、溶接工は完全な防護マスクを必要とし、人体のやけどを防止する。
(3)通風条件:フラックス入りワイヤアーク溶接はいずれも有害ガスと煙を発生するため、溶接現場で良好な通風条件を維持しなければならない。十分な外気の流通がない場合は、排気設備を使用するか、窓とドアを開ける必要があります。
(4)緊急救援設備:溶接現場に緊急救援設備、例えば消火器、救急箱などを配備し、不測の事態が発生した時に使用する。
(5)溶接領域の準備:溶接操作を行う前に、作業者は溶接領域が清潔であることを確保し、可燃物と可燃物を除去しなければならない。
(6)電源と設備の検査:溶接操作の前に、労働者は電源と設備が正常に動作しているかどうかを検査し、電源過負荷と設備故障による安全上の危険を避けるべきである。
(7)アーク反射に注目:二酸化炭素ガス保護溶接とフラックス入りワイヤアーク溶接の操作時、アークは強い光放射と紫外線を発生する可能性がある。そのため、溶接工はアーク反射領域に直接露出しないように注意し、必要に応じて放射線防止ゴーグルや遮蔽板を使用する必要がある。
(8)火器の使用:溶接操作を行う時、燃焼しやすい材料と容器から離れなければならない。溶接現場には専門の溶接台、電気ドラム、溶接網などを備え、安全に溶接設備と材料を貯蔵し、堆積する必要がある。
(9)安全操作技術:溶接操作を行う時、労働者は正しい操作手順に従って行い、設備と工具の使用方法を熟知し、溶接規範と基準を守り、そして焦りと不注意による操作ミスを避けるべきである。
(10)溶接終了後の処理:溶接操作が完了した後、直ちに溶接設備と電源をオフにし、溶接区域を整理し、溶接設備と材料を適切に保管しなければならない。
(11)訓練と意識の向上:溶接操作の安全性を確保するために、労働者は相応の訓練を受けて安全意識を高め、定期的に安全検査とメンテナンスを行い、設備と工具の正常な運行を確保する。
2.4 サブマージアーク溶接(SAW)
埋め込みアーク溶接(分自動、半制動)アークはフラックス領域で燃焼し、粒状フラックスを利用して、金属溶融池の被覆層として、空気を遮断して溶融池に入らないようにする。ワイヤはワイヤ送給機構によってアーク領域に連続的に送給され、アークの溶接方向、移動速度は手作業または機械で完成する。中厚板材料の炭素鋼、低合金鋼、ステンレス鋼、銅などの直溶接及び規則溶接の溶接に適用する。
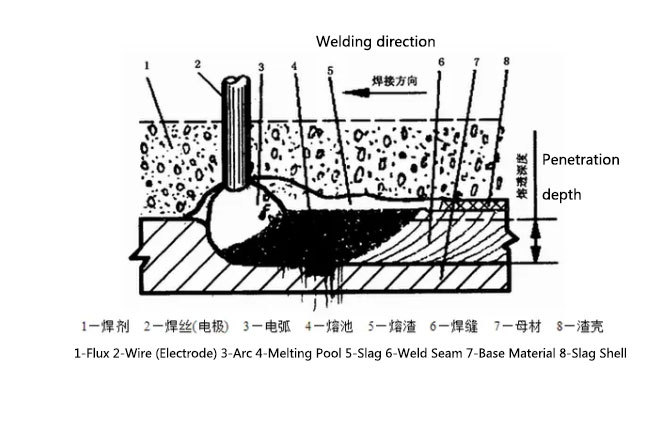
2.4.1 サブマージアーク溶接の利点
(1)使用する溶接電流が大きく、その分入力電力が大きい。フラックスとスラグの断熱作用を加えると、熱効率が高く、溶融深度が大きい。ワークピースの開先は小さく、充填金属量を減らすことができます。モノフィラメント埋め込みアーク溶接は、ワークが開先しない場合、一度に20 mm溶融することができる。
(2)溶接速度が高く、厚さ8〜10 mmの鋼板の突合せ溶接を例にして、単線埋め込みアーク溶接速度は50〜80 cm/minに達することができ、手動アーク溶接は10〜13 cm/minを超えない。
(3)フラックスの存在は、溶融金属と空気との接触を分離するだけでなく、溶融池の金属をゆっくりと凝固させることができる。液体金属と溶融したフラックスとの間には冶金反応を行う時間が多く、溶接ビードに気孔、ひび割れなどの欠陥が発生する可能性が減少した。フラックスはまた、溶接金属に合金元素を補充することができ、溶接金属の力学的性能を高めることができる。
(4)風のある環境で溶接する場合、埋め込みアーク溶接の保護効果は他のアーク溶接方法より良い。
(5)自動溶接時、溶接パラメータは自動調整により安定して保持できる。手動アーク溶接に比べて、溶接品質の溶接技術レベルへの依存度は大幅に低下することができる。
(6)アーク光放射がなく、労働条件がよい。
2.4.2 サブマージアーク溶接の欠点
(1)粒状フラックスを用いるため、この溶接方法は一般的に平溶接位置にのみ適用される。その他の位置溶接は特殊な措置を採用して溶接剤が溶接領域をカバーできることを保証する必要がある。
(2)アークと開先の相対位置を直接観察することができず、溶接自動追跡装置を採用していないと溶接偏移しやすい。
(3)埋め込みアーク溶接アークの電界強度が大きく、電流が100 A未満の場合アークが不安定であるため、厚さが1 mm未満の薄板の溶接には適さない。
2.4.3 サブマージアーク溶接の応用
埋込みアーク溶接は溶融深さが大きく、生産性が高く、機械化操作の程度が高いため、溶接中の厚板構造の長い溶接に適している。造船、ボイラーと圧力容器、橋梁、クレーン機械、鉄道車両、建設機械、重機と冶金機械、原子力発電所構造、海洋構造などの製造部門で広く応用されており、現在の溶接生産で最も一般的に使用されている溶接方法の一つである。
埋め込みアーク溶接は、金属構造中の部材の接続に加えて、基体金属表面に耐摩耗性または耐腐食性の合金層を積層溶接することができる。溶接冶金技術と溶接材料の生産技術の発展に伴い、埋め込みアーク溶接エネルギー溶接の材料は炭素構造鋼から低合金構造鋼、ステンレス鋼、耐熱鋼など及びニッケル基合金、チタン合金、銅合金などの一部の非鉄金属に発展した。
2.5 タングステン極不活性ガスシールド溶接GTAW(TIG)
TIG溶接(タングステン極不活性ガス溶接)は前世紀半ば頃に発展した。このプロセスでは、電極は金属を充填するのと同じではなく、必要に応じて充填金属の添加を独立に制御できることを意味します。TIG溶接は唯一の電極とワークがアークを発生して金属を溶融する溶接方法である。
溶接電源は高周波電流を発生し、ワークに接触しないアークを発生するためにこの電流を必要とする。この技術は通常、パイプ溶接用途に用いられ、溶接パスを完璧に制御できることから特に人気がある。TIG溶接には手動、半自動、または全自動バージョンがあります。
2.5.1 タングステン極
タングステン極はTIG溶接の核心である。タングステンは金属周期表内のすべての純金属の中で最も融点の高い元素であり、その融点は3380℃である。これは、タングステン針がアーク加熱を発生して材料を溶融する際に、それ自体が溶融しないことを意味する。タングステン極は焼結プロセスによって製造され、酸化剤を添加してタングステン合金を形成することによって性能が向上し、元素によってタングステン極の端部は異なる色を示している。
純タングステン(WP)(緑色)/平滑、球形針/直流モードのアーク発生しにくい/負荷電流能力差
トリウムタングステン(WS 2)(青色)/全材質に適用可能/アーク発生性能良好/耐用年数比WT(トリウムタングステン電極)またはWC(セリウムタングステン電極)長セリウムタングステン(WC 20)(灰色)/全材質に適用可能/アーク発生性能良好
ランタンタングステン(WL 20)(青色)/ガドリニウムタングステンまたはセリウムタングステンに比べて耐用年数が長い/起弧性能が悪い
2.5.2 利点
スプラッシュなし
放射線探傷検査
全位置溶接に適用
溶接成形が美しく、品質が高い
2.5.3 欠点
溶接工の溶接技能に依存する
溶接速度が遅い
溶接前の準備作業の要求が高く、溶接ビード表面のさびを完全に除去しなければならない
不適合厚板溶接
2.5.4 適用範囲
TIG溶接は上述の利点があるため、工業と生活の中で広く応用されている。TIG溶接は以下のいくつかの態様で使用することができる:
炭素鋼、ステンレス鋼、アルミニウム合金、ニッケル合金、銅合金、チタン合金などの各種金属材料を溶接することができる。
各種厚さのワークを溶接することができ、0.1 mmから10 mm以上まで高品質の溶接を実現することができる。
平板、立板、横角、縦角などを含む様々な位置のワークを溶接することができる。
航空宇宙、原子力、自動車製造、造船、化学工業、医療機器など、さまざまな業界や分野で使用することができる。
2.5.5 TIG溶接システムの構成

2.6 高エネルギー密度溶接(HED)
これらの溶接技術は、必要な設備が非常に高価(数百万ユーロ)であるため、一般的ではありません。現在、高エネルギー密度溶接技術は主に3種類がある:プラズマ溶接、電子ビーム溶接とレーザービーム溶接。これらの技術は多かれ少なかれ同じ利点を持っている:それらは非常に高速なプロセスであり、非常に大きな厚さを溶接することができる。ガスのエネルギーはアークを凝集させるために使用され、プラズマ溶接性能を向上させる。必要に応じて、フィラーワイヤを追加することができます。レーザービーム溶接は医療や電子などの分野で人気がある。電子ビーム溶接には真空チャンバが必要で、設置にはかなりの時間がかかります。
高エネルギー密度溶融溶接は必ずしも圧力溶接と同等ではなく、2つの異なる概念である。
高エネルギー密度溶融溶接(High Energy Density Welding)は、レーザビーム、電子ビームなどの高エネルギー源から発生する高エネルギー流密度を用いて材料を加熱し、溶融させて溶接ビードを形成する溶接プロセスの一種である。この溶接プロセスは、急速な溶融と接続を可能にするために、短い時間で大量の熱を提供します。この溶接方法は高精度、高速度、高効率の溶接応用によく用いられる。
圧力溶接(Pressure Welding)は、一定の圧力を加えて2つ以上の金属表面を接触させ、熱を交流させ、溶接接続を発生させる溶接方法である。一般的な圧力溶接方法には、摩擦溶接、抵抗溶接、爆発溶接などが含まれる。圧力溶接は通常、追加の熱源を必要とせず、圧力と熱の相互作用によって溶接を実現する。
場合によっては、高エネルギー密度溶融溶接を圧力溶接と組み合わせて使用して、より強い溶接接続を生成することもできます。例えば、レーザー溶接では、溶接の品質と強度を強化するために追加の圧力を加えることができる。
したがって、高エネルギー密度溶融溶接と圧力溶接はいずれも溶接方法であるが、完全に同等ではなく、溶接原理と応用の面で異なる。
2.7 ろう付け
ろう付けとは、ろう材の融点より低いろう材とろう材を同時にろう材溶融温度に加熱した後、固体ワークの隙間を液体ろう材で充填して金属を接続する溶接方法である。ろう付けの際には、まず母材の接触面の酸化膜と油汚れを除去し、ろう材が溶融した後に毛細管が作用し、ろう材の濡れ性と毛細管流動性を増加させるのに有利である。ろう付けはろう付けの融点によって、ろう付けとろう付けに分けられる。
2.7.1 利点
(1)ろう付け加熱温度が低く、母材組織と性励起への影響が小さい、
(2)ろう付け継手は平らで滑らかで、外形が美しい、
(3)溶接部品の変形が小さく、特に均一加熱(例えば炉中ろう付け)のろう付け方法を採用し、溶接部品の変形を最小限に抑えることができ、溶接部品の寸法精度を保証しやすい、
(4)一部のろう付け方法は一度に数十本または百本のろう縫いに溶接でき、生産性が高い、
(5)異種金属又は合金、金属と非金属との接続を実現することができる。
2.7.2 欠点
ろう付け継手の強度は比較的に低く、耐熱能力は比較的に悪く、母材とろう材成分の差が大きいことによる電気化学腐食により耐食力が比較的に悪く、組み立て要求が比較的に高い。
2.7.3 適用範囲
ろう付けは一般的な鋼構造と重荷、動キャリアの溶接には適していない。主に精密計器、電気部品、異種金属部材及び複雑な薄板構造、例えばサンドイッチ部材、ハニカム構造などの製造に用いられ、また各種異線と硬質合金工具のろう付けにもよく用いられる。
2.8 すいちゅうようせつ
水中溶接は水の存在によって溶接過程がより複雑になり、また様々な陸上溶接には遭遇していない問題が発生し、世界各国で応用・研究されている水中溶接方法は種類が多く、応用が比較的成熟しているのはアーク溶接である。水中溶接技術の発展に伴い、一般的な湿式水中溶接、局所乾式水中溶接、乾式水中溶接のほか、新たな水中溶接方法が出現した。しかし、各国の海洋開発の将来性から見ると、水中溶接の研究は情勢の発展の需要にはるかに適応できない。そのため、この方面の研究を強化することは、現在に対しても将来に対しても、非常に意義のある仕事になるだろう。
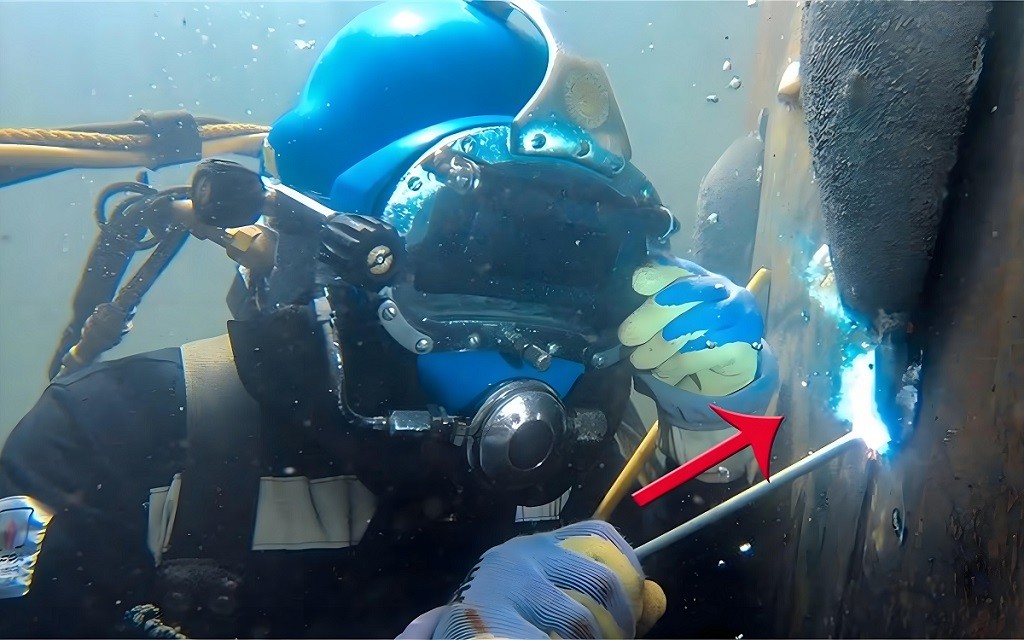